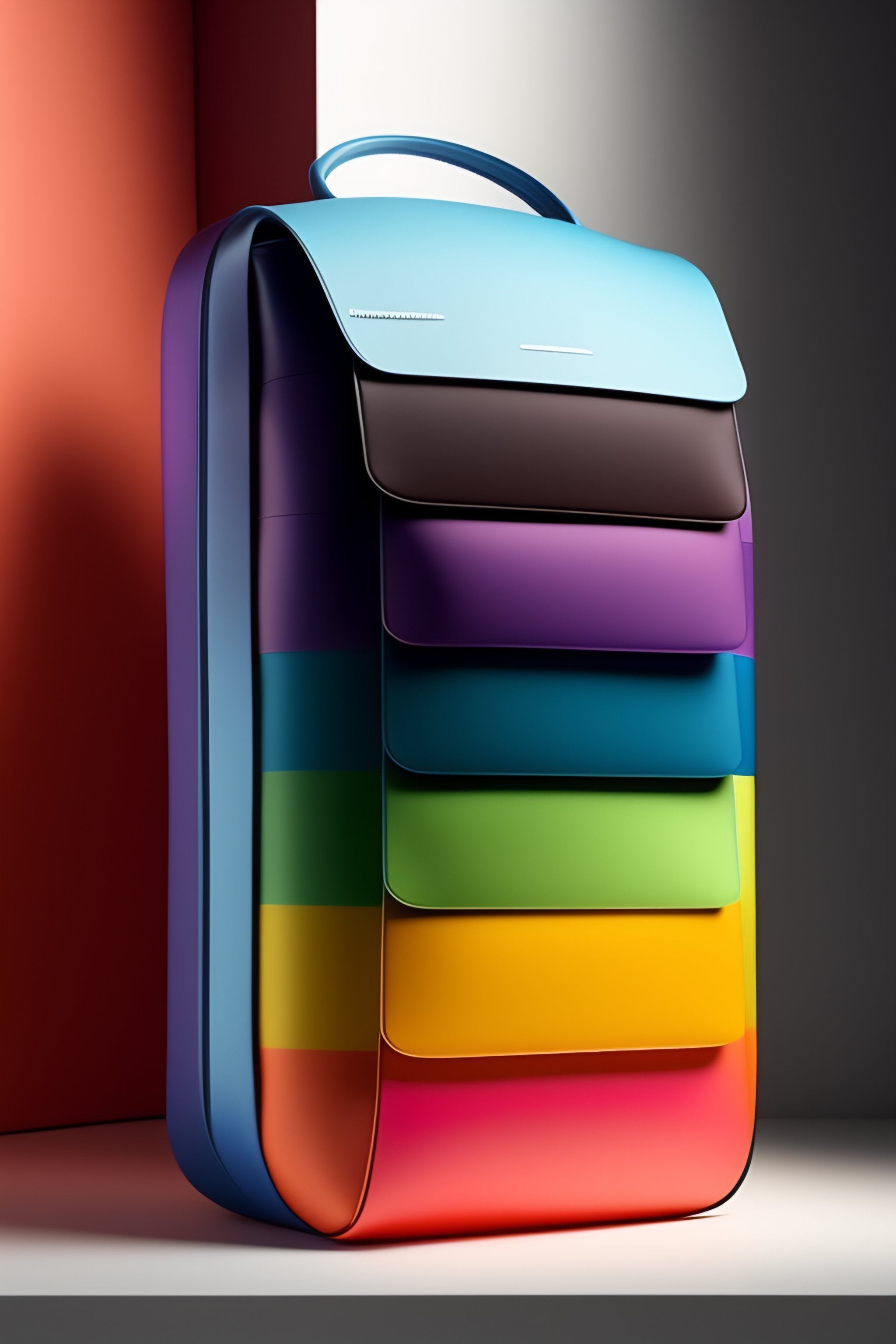
Slip masterbatch is a specialized additive used in the plastics industry to improve the slip or sliding properties of plastic materials. It is designed to reduce the coefficient of friction between surfaces, making the plastic surface smoother and more slippery.
Appearance | Granule/Pellets |
---|---|
Color | Natural |
Carrier Resin | PE |
Active Ingredients | ≈ 8 % Erucamide |
Thermal Stabilizer | Yes |
Melf Flow Index | ≈ 3.5 gr/10min. (@ 190 °C , 2.16 kg) |
Specific Density | ≈ 0.91 gr/cm3 |
Appearance | Granule/Pellets |
---|---|
Color | Natural |
Carrier Resin | PP |
Active Ingredients | ≈ 8 % Erucamide |
Thermal Stabilizer | Yes |
Melf Flow Index | ≈ 5.5 gr/10min. (@ 190 °C , 2.16 kg) |
Specific Density | ≈ 0.89 gr/cm3 |
Slip masterbatch typically contains additives such as long-chain fatty amides, erucamide, or other slip agents dispersed in a carrier resin that is compatible with the base polymer. The carrier resin ensures uniform distribution of the slip agents throughout the plastic matrix.
Slip masterbatch reduces the friction between plastic surfaces, making them less sticky and easier to slide over one another. It helps to improve the slip characteristics of plastic films, sheets, and molded parts, enabling easier processing, handling, and packaging.
The slip additives in the masterbatch decrease the coefficient of friction between the plastic surfaces, thereby reducing the resistance to movement. This results in improved slip performance and reduced adhesion between the plastic and other surfaces.
Slip masterbatch should be compatible with the base polymer to ensure effective dispersion and optimal slip performance. Compatibility testing is necessary to evaluate the performance and compatibility of the masterbatch in the specific plastic matrix.
The concentration of slip masterbatch required depends on factors such as the desired level of slip properties, the specific polymer type, and the intended application. It is important to determine the appropriate concentration through testing to achieve the desired slip performance without adversely affecting other properties of the plastic.
Slip masterbatch is typically added to the plastic resin during the compounding or extrusion process. The masterbatch is thoroughly mixed with the base resin to ensure uniform distribution of the slip additives throughout the final product.
Slip masterbatch finds applications in various industries, including packaging, automotive, and consumer goods, where slip properties are desirable. It can be used to improve the processing and handling of plastic films, prevent blocking or sticking, facilitate the easy release of products from molds, and enhance the overall functionality and performance of plastic products.
The information provided herein is based on our current knowledge and is intended to offer general guidance on products and their applications. It should not be construed as a guarantee of specific product properties or their suitability for a particular purpose. Due to the wide variability of conditions in product usage, which are beyond MKEY's control, users must independently assess whether MKEY products are suitable for their intended applications prior to use.
The quality of our products is warranted in accordance with our General Terms and Conditions of Sale, which are currently in effect or may be updated in the future. Technical information, test data, and advice provided by MKEY personnel are based on our best knowledge and reliable tests. However, it is assumed that recipients of such information possess the necessary expertise and technical skills to analyze test methods and conditions, as well as handle and utilize raw polymers and related compounding ingredients effectively.